Contents
5 Types of Risk Assessments & How to Use Them
29 October 2024 - Evotix
Risk assessments are often a legal requirement, essential for ensuring workplace safety and compliance. Simply put, a risk assessment helps identify hazards and potential risks within a work environment, providing effective strategies to mitigate or eliminate these threats, ultimately promoting a safe and secure workplace for everyone.
Hazards in the workplace vary widely, from physical dangers to chemical exposures and beyond—so risk assessments must be adaptable to address these different challenges. Using the correct type of risk assessment for each situation is key to capturing the unique risks that exist within any given workplace. Often, a blend of multiple assessment types provides the most thorough and effective evaluation, allowing you to pull the most relevant aspects from each into one cohesive approach.
In this guide, we’ll explore the five main types of risk assessments and how you can use them to support comprehensive health and safety management in your organization.
Stages of a risk assessment
To ensure that your risk assessment is effective and comprehensive, it should encompass the following six key steps:
1. Plan
Good planning is integral to ensuring you get your risk assessment off to a strong start. Before conducting your risk assessment, consider these four elements noted by OSHA:
-
What are you assessing? (A piece of equipment, process or workplace area?)
-
What resources do you need to carry out the assessment? (Tools or equipment?)
-
Who is involved? (Workers, managers, supervisors or suppliers?)
-
What laws, regulations and internal policies do you need to comply with?
2. Identify hazards
This involves a walkthrough of your workspace to identify anything that could reasonably be expected to cause harm. Involving other employees in this stage could be helpful, as they may have noticed things that don’t immediately stick out at you.
While assessing the workplace, ensure you consider long-term hazards to health (like high noise levels or exposure to harmful substances) and safety hazards.
Once you’ve identified each hazard, make sure you understand how it could harm someone or the environment – as this will help you identify the most impactful way of managing the risk further down the line.
3. Evaluate identified risks
Now that hazards have been identified, it’s time to decide how to handle them.
Under the OSH Act, employers are obligated to maintain workplaces that are free from known hazards that could pose risks to their employees. One of the most effective strategies to achieve this is by benchmarking your current practices against industry best standards.
First, assess the controls you currently have in place and how they’re implemented. Compare these controls against identified best practices to see if there’s room for improvement.
4. Take action
Once you’ve identified specific areas for improvement to reduce risks, it's time to act. HSE suggests applying the following principles:
-
Try a less risky option (for example, switching to a less hazardous chemical)
-
Prevent access to the hazard (such as guarding)
-
Organize work to reduce exposure to the hazard (for example, by placing barriers between pedestrians and traffic)
-
Issue personal protective equipment (gloves, goggles, etc)
-
Provide emergency areas (like first aid or eye wash stations)
5. Record findings and actions taken
At this stage, you should write down the risk assessment results and share them across your organization to encourage all employees to put these new actions into practice.
Write down your results as simply as possible, for example: “Fire door blocked: area cleared, staff instructed, weekly checks.”
While recording your risk assessment findings, you should be able to demonstrate:
-
That you've identified the hazards
-
That you’ve decided who could be harmed
-
How you plan to eliminate/minimize the risks and hazards
6. Review process
Workplaces are constantly evolving, with new processes introducing new risks and hazards. Therefore, it’s essential to regularly review your practices and update the relevant risk assessment forms as needed.
What are the different types of risk assessment?
Risk assessments come in many different forms, but here are the five most common:
1. Qualitative risk assessment
Qualitative risk assessments are the most frequently used risk assessments for companies in high-risk industries. Assessments of this kind measure the severity of a risk. In most cases, qualitative risk assessments are used to determine the severity of multiple risks at once. These assessments rely on the perceptions and judgments of an individual—often an expert in the company’s field or a member of management.
When these assessments are employed, the assessor’s personal experience, observations and interviews are used to gather qualitative data, which are then analyzed with the goal of determining the severity of multiple risks.
The severity of a risk can be determined using the following formula: impact describes how severely a risk could negatively affect a project and likelihood describes how often the risk is likely to occur.
Severity = Impact x Likelihood
When the information is presented, it is organized either into categories or a graph known as a Qualitative Risk Assessment Matrix. Both schemes are based on severity. Categories are labeled High, Medium and Low—or, depending on the company’s preferences, Green, Amber and Red (GAR). In a Qualitative Assessment Matrix, one axis is labeled ‘Impact’ and the other ‘Likelihood,’ and plot points (risks) are charted in according to severity. Presentations allow the company to quickly identify the highest-severity risks.
When compared to quantitative risk assessments, qualitative risk assessments can often be more practical. These assessments are cheaper and faster and allow for the comparative analysis of multiple risks. They don’t require gathering vast amounts of numerical data; instead, qualitative risk assessments rely only on the judgments of one person. Most importantly, qualitative risk assessments enable companies to invent solutions for the most severe risks quickly and efficiently.
2. Quantitative risk assessment
A quantitative risk assessment involves determining the severity and likelihood of a risk by giving it a number. This type of assessment aims to gauge how much the impact of the risk will cost an organization. Rather than referring to a risk as high, medium or low, a quantitative risk assessment assigns a digit to the risk.
The main difference between a qualitative and quantitative risk is that rather than being based on a person’s judgment, as a qualitative risk is, a quantitative risk analysis relies on hard data. Another contrast between the two is how each process values risk. While in a qualitative risk assessment, an innocuous risk may be rated 'low,' the same risk will be given a low percentage in a quantitative assessment to indicate the possibility of it occurring or causing harm.
A scenario in which quantitative risk assessments are commonly used is to predict the likelihood of a fire or explosion when using harmful chemicals. Project managers can select one of the following methods for quantitative risk assessment:
-
Failure Mode and Effects Analytics (FMEA) - anticipating shortcomings in business processes and coming up with ways to mitigate their impact on customers
-
Business Impact Analysis (BIA) - identifies and evaluates impact of natural disasters and sets aside investment in recovery, prevention and mitigation strategies for organizations effected
-
Expected Monetary Value (EMV) - this method involves senior management carrying out the following equation: Probability in % of Risk Occurring x Cost of Impact in Preferred Currency
Results can also be recorded in a risk assessment matrix (or any other form of an intuitive graphical report) to communicate outstanding hazards to stakeholders. Although this method involves the assignment of numbers to the degree of risk, it is technically a qualitative method in that it's based on the assessor’s judgment.
3. Generic risk assessment
Generic risk assessments include assessing a broad range of specific workplace activities. Generic risk assessments are most useful regarding repetitive tasks which are consistent in application for organizations, such as:
-
Working in confined spaces
-
Working at heights
-
Fire emergency responses
-
Manual handling
-
Use of different pieces of machinery
-
Use of display equipment
Carrying out generic risk assessments in these circumstances often proves useful for large organizations, as the findings can then be applied equally to similar tasks across different areas of the workplace or different sites altogether.
This can be done, for example, with the act of locking out a piece of machinery commonly used across several areas of a manufacturing site or installing electrical equipment.
4. Site-specific risk assessment
As the name suggests, a site-specific assessment places a particular site, environment and team of employees performing the task under the microscope to ensure everything is running as safely as it should be.
The main difference between generic and site-specific assessments is that generic assessments focus on common hazards related to routine activities, like roofing work, while site-specific assessments address unique hazards in a particular location with tailored controls—for instance, valley gutters on a roofing site.
Given the connection between both assessments on a roofing site, it often makes sense to follow a generic assessment with a site-specific one, allowing inspectors or management to focus more closely on specific areas of concern.
Other examples of hazards that could be picked up by a site-specific risk assessment that wouldn’t otherwise be recognized by a generic risk assessment on roofing works include potential asbestos from cement roof sheets or glazing rope or trip hazards, including lightning conductors or drain vents.
5. Dynamic risk assessment
A dynamic risk assessment evaluates risks in rapidly changing, uncertain and often high-risk environments. In contrast to formal risk assessments, which are a legal requirement and should be carried out as a precursor to any task being done, dynamic risk assessments are normally carried out by a lone worker when they arrive in a new environment. There may also be circumstances where a person’s regular working environment changes, making generic or even site-specific risk assessments obsolete and presenting the need for a dynamic approach.
It’s important that the person carrying out a dynamic assessment understands that not every risk can be prepared for because of the nature of these environments. It would be expected that the person conducting a dynamic risk assessment has the experience required to make an informed judgment call if a situation becomes too dangerous – such as delaying a task until safe equipment is sourced.
An example of a dynamic risk assessment includes a construction worker visiting a new worksite and assessing the hazards he hasn’t seen before, having not been on that site. Not to be mistaken as a replacement for formal risk assessments, dynamic risk assessments are to be carried out alongside them to identify any unknown risks.
How Evotix can help
While manual risk assessments are possible, they’re often inefficient for proactive hazard management across an organization. Using software streamlines the process by managing data from all areas of the organization in one place. The software highlights high-risk activities through matrices, enabling rapid control implementation and action tracking to ensure controls are effective. With centralized form storage, it allows workers across departments to conduct and review assessments, keeping everyone informed about hazards.
Understanding different types of risk assessments is essential for a safe, productive workplace. Involve employees in the process to ensure they stay updated on solutions for completing tasks safely.
Want to learn more about how we can help streamline your risk management processes?
RELATED BLOGS
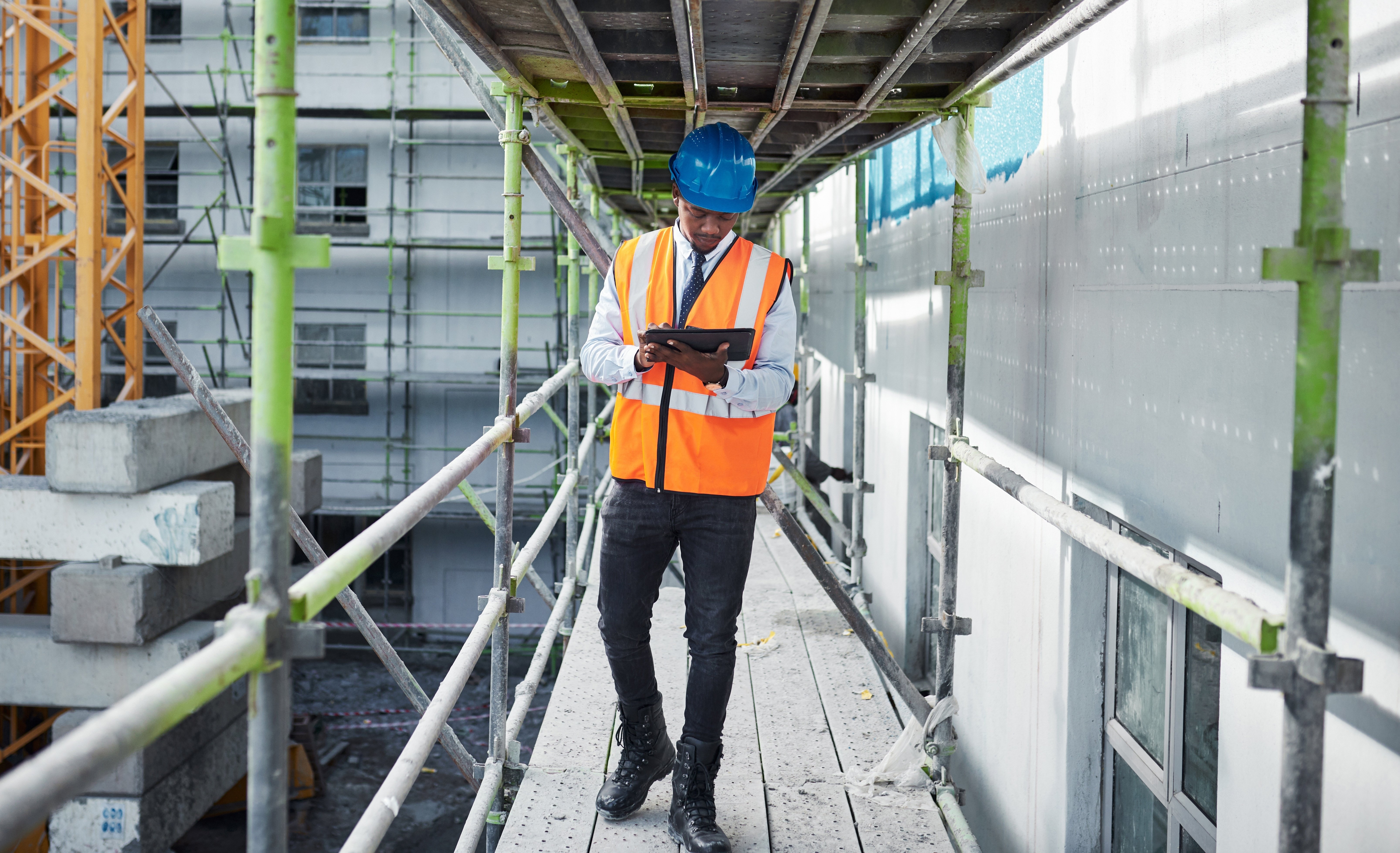
7 Benefits of Conducting a Risk Assessment
1 November 2024 - Evotix
Risk assessments aren’t just about clipboards and checking boxes; they bring real, irreplaceable value to the workplace by helping identify current and potential hazards and risks in the workplace..
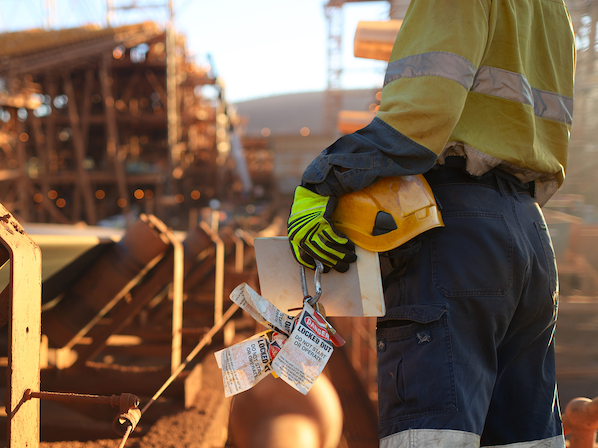
What is a Risk Assessment?
20 October 2022 - Evotix
So first things first, what exactly is a risk assessment?
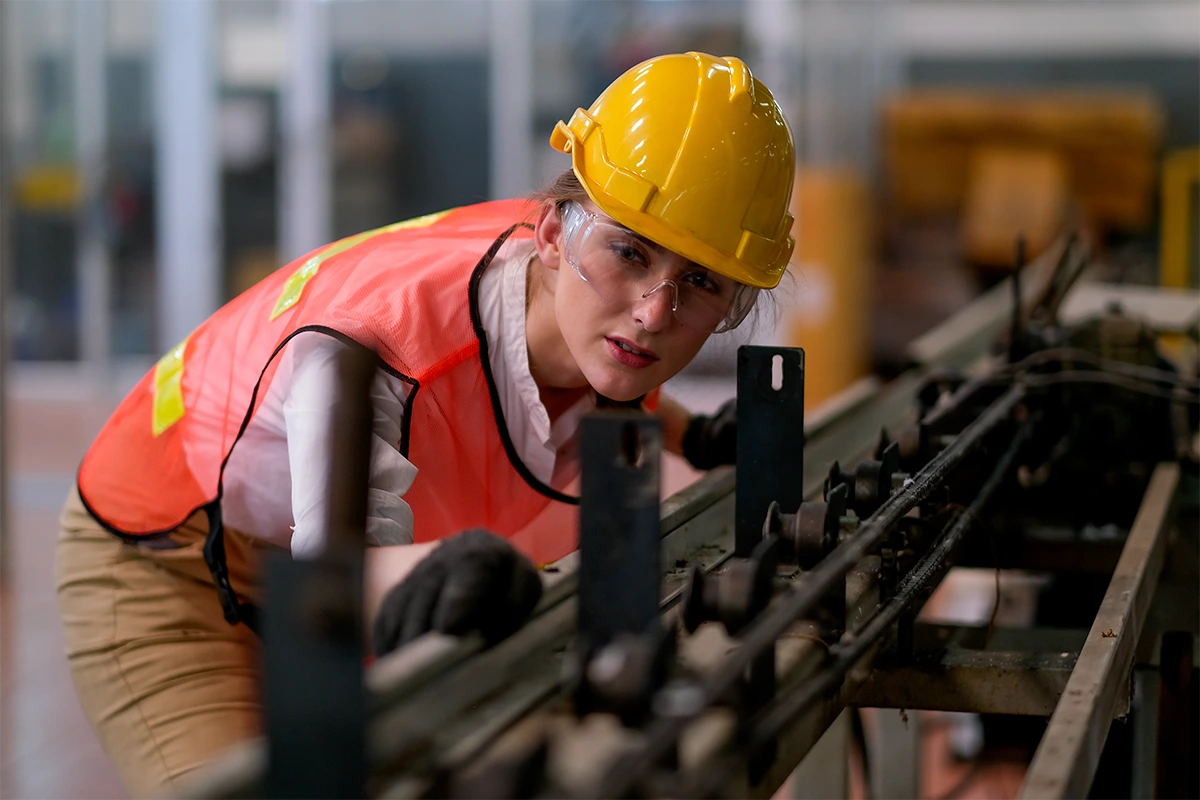
10 Reasons Why Risk Management Is Essential
3 October 2024 - Evotix
Risks are a daily occurrence in most businesses, so a system must be put in place to effectively control them. Risks inherently turn into incidents if not dealt with properly – not only harming..