Contents
The Importance of Safety in the Manufacturing Industry
27 November 2024 - Evotix
While industries like construction, fishing or hunting often top the list for serious workplace incidents, manufacturing holds a unique and concerning position. Despite employing a smaller percentage of the workforce, it accounts for a disproportionately high number of workplace injuries and illnesses.
Why? Because manufacturing workers face daily interactions with heavy machinery, hazardous materials and dangerous substances. These tools are essential for the job, but they also come with serious risks, from severe injuries to long-term health effects.
For example, workers who interact with solvents, lubricants or other chemicals may be at risk of burns, rashes and respiratory issues. Additionally, workers who interact with heavy machinery may be at risk of injuries ranging from bruises to puncture wounds to loss of limbs.
On the bright side, incidents like these can be prevented. With an increased investment of time, energy and money in health and safety for the workplace, organizations in this industry can significantly reduce the number of injuries, illnesses and deaths that occur.
Understanding these risks is key to creating safer, healthier workplaces. Let’s dive into the challenges and solutions.
Why is health and safety important in manufacturing?
It’s a no-brainer that health and safety practices must be at the heart of any manufacturer’s daily operations. But the reasons for maintaining a strong health and safety policy go beyond protecting employees in the workplace and complying with regulations.
Too often, companies view health and safety programs as a drain on time and resources, prioritizing productivity, quality and cost-effectiveness instead. But here’s the catch: neglecting safety doesn’t just harm employees—it also undermines those very business goals.
The truth? Health and safety isn’t a competing priority; it’s a key driver of success. Studies show that prioritizing workplace safety boosts productivity, ensures consistent quality and reduces costs. It’s a win-win for employees and the bottom line. OSHA’s Business Case for Safety and Health offers research, statistics and several case studies on the substantial return on investment that accompanies a focus on health and safety.
Here are just a few of the benefits of a dedicated health and safety program in a manufacturing workplace:
-
Reduces incidents such as illness, injury and death
-
Ensures compliance with regulations
-
Increases productivity
-
Ensures quality
-
Boosts employee morale
-
Minimizes indirect costs related to incidents, such as regulatory fines, workers’ compensation claims, operational costs and legal fees
The costs of neglecting safety in manufacturing
Failing to implement a comprehensive health and safety program isn’t the only way companies can neglect health and safety in the workplace. When businesses fail to procure safe machinery, provide adequate PPE, provide employees with proper training or instill a culture that promotes health and safety, incidents are more likely to occur.
When an incident occurs as a result of poor health and safety practices, a variety of costs can be inflicted on a manufacturing company. Many of these costs may be direct and immediate, but more may be indirect and spread over time.
Imagine this: an employee uses an unguarded machine, their sleeve gets caught and they injure their arm. The fallout for the employer can be significant, including:
-
Direct costs: covering workers' compensation, regulatory fines, hiring and training a replacement, repairing equipment, addressing lost production, legal fees, court costs and higher liability insurance premiums.
-
Indirect costs: damage to the company’s reputation, lost time during investigations and site cleanup and decreased employee morale and productivity.
The lesson is clear: investing in a strong health and safety program, staying current with regulations and equipping employees with proper training and PPE costs far less than dealing with the aftermath of an incident. Proactive safety measures aren’t just smart—they’re essential.
4 key steps to improving health and safety in the manufacturing industry
It may sound like a complex task but improving health and safety in a manufacturing company can be broken down into four key steps. These include creating a culture that promotes health and safety, providing employees with adequate safety tools and training and implementing a comprehensive safety program. When these steps are executed well, they can reduce incidents, increase productivity and save money.
1) Create a culture that promotes health and safety
Creating a business culture that promotes health and safety is a crucial step toward better safety practices. This can be done by keeping employees regularly engaged with health and safety, simplifying practices and procedures, rewarding positive behaviors, maintaining open communication and keeping management involved.
2) Make proper use of safety tools
When we talk about "safety tools," we’re not just talking about PPE. While providing employees with essentials like protective clothing, footwear and helmets is crucial, safety tools go far beyond that. They include your organization’s health and safety systems, policies, practices and even software solutions. These tools work together to create a safer, more efficient workplace. To truly enhance health and safety across your organization, make full use of all these tools—not just the ones you can wear.
3) Provide health and safety training
With such a high degree of risk involved in manufacturing employees’ work, managers need to ensure that employees receive adequate safety training in order to carry out their jobs safely. There must also be a system in place that allows the employer to track which training courses/modules have been completed and provide employees with easy access to training resources. One way to ensure that these steps are taken is by using a health and safety training app.
4) Integrate a detailed health and safety program
To ensure that employers are able to take a holistic view of the safety practices and measures across their workplace, there must be a detailed, comprehensive safety program in place. Manufacturing EHS software can provide a streamlined approach to ensure that every aspect of safety in the workplace is monitored and measured accordingly.
Maintaining a strong health and safety system is a necessity in the manufacturing industry. Employees interacting regularly with dangerous machinery, substances and materials need protection, and employers need to ensure that their operations follow regulations. Additionally, keeping focused on health and safety can increase productivity, ensure quality, boost employee morale and minimize indirect costs related to incidents.
To learn more about how Evotix supports the safety and efficiency of manufacturing companies, click below!
RELATED BLOGS
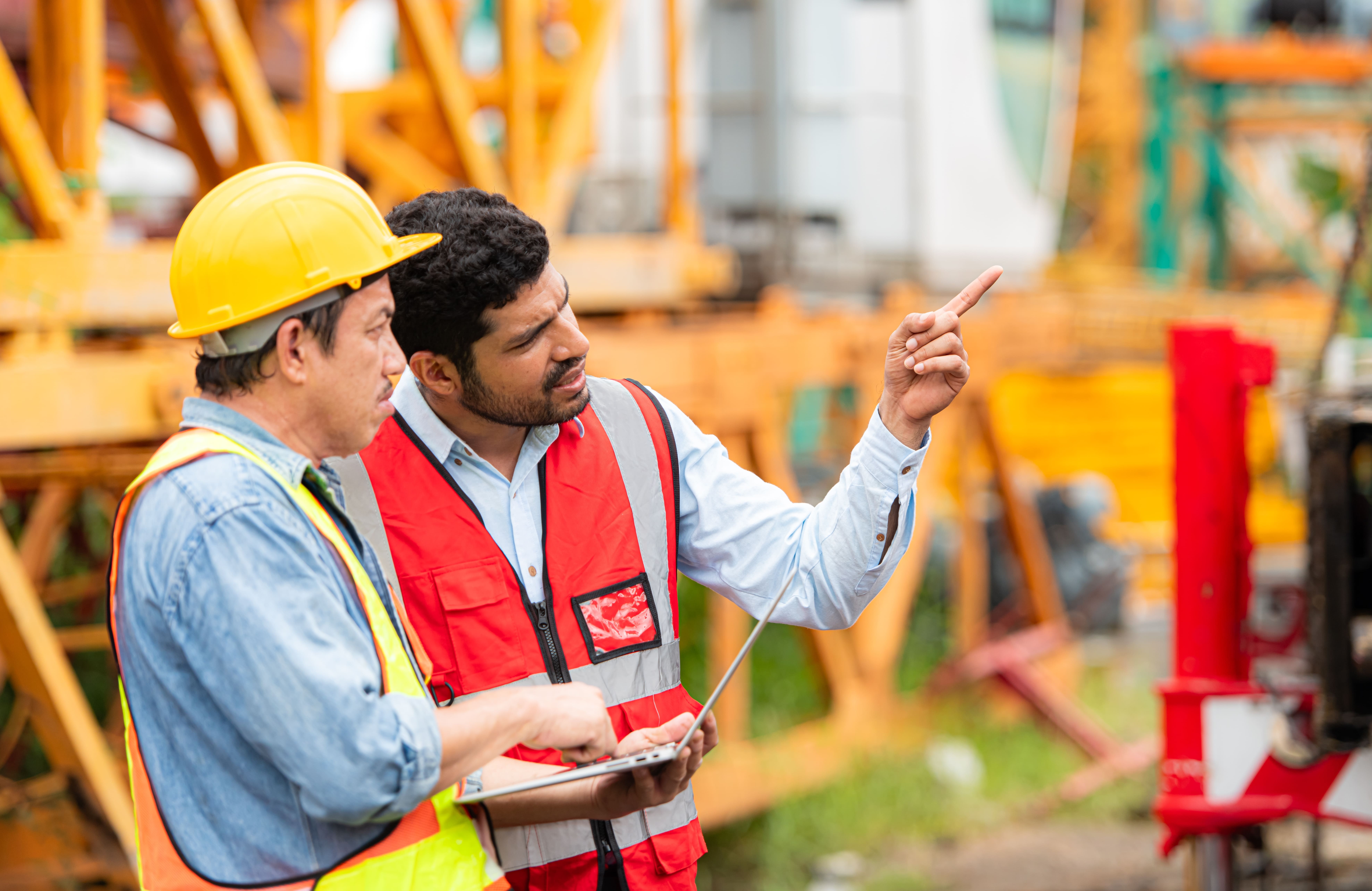
Who Benefits Most From Safety Regulations? The Ripple Effect of Workplace Safety
22 May 2025 - Evotix
With a growing number of workplace safety regulations to follow, it's easy to view them as a box-checking exercise or a hurdle to jump through. However, it raises a fair question: Who are these..
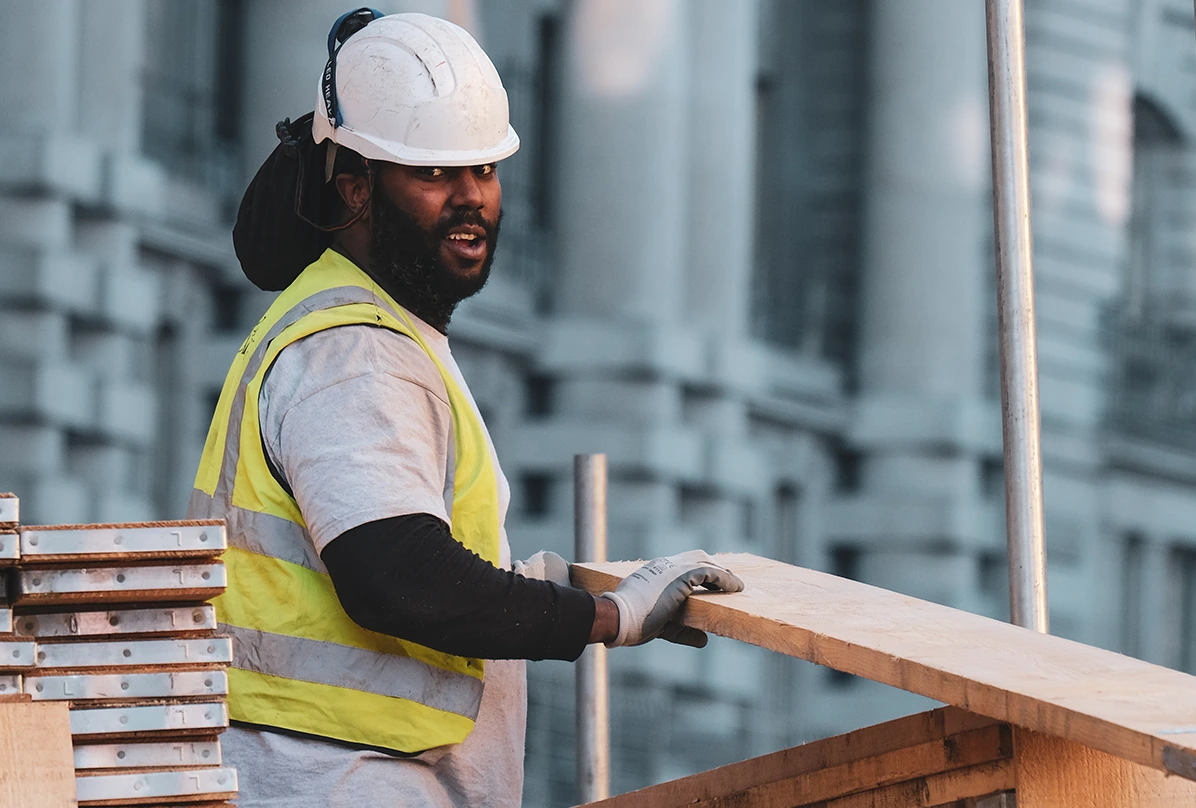
The Importance of Health & Safety in Construction
17 November 2022 - Evotix
Construction is an inherently dangerous profession. From working at heights, to operating heavy machinery and using tools, the tasks undertaken by the typical construction worker are more..
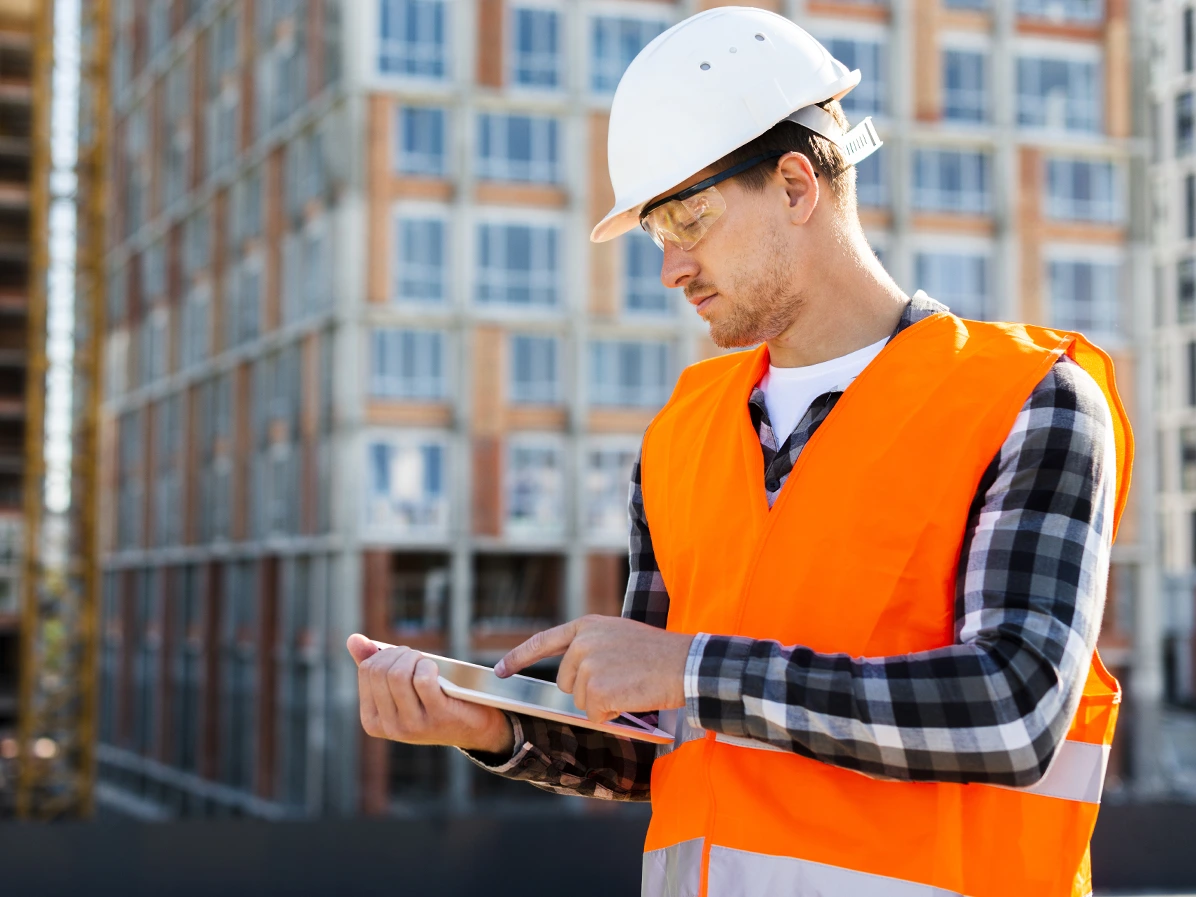
What Is Contractor Safety Management?
21 November 2024 - Evotix
Hiring skilled contractors to address workforce gaps is becoming increasingly common. However, as temporary team members, contractors often bring varying levels of skills, qualifications and..