Contents
The 5 Key Components of a Safety Audit
14 November 2024 - Evotix
Safety audits are essential for upholding health and safety standards across your organization. Beyond meeting legal requirements, they help proactively identify and address potential hazards that, if overlooked, could result in serious incidents or even fatalities. Additionally, audits are instrumental in refining your safety strategy by highlighting areas for improvement within your current practices, creating a stronger, more resilient safety framework.
To get the most out of safety audits, organizations should follow best practices to turn valuable insights into real improvements.
In this guide, we’ll cover the key elements of an effective workplace safety audit that goes beyond simple checklists to provide clear, actionable steps for a safer workplace.
1. Ensuring consistency and timeliness
Safety audits should not be confused with routine inspections, nor should they be conducted as frequently. Audits involve a thorough examination of an organization's safety policies, programs and processes, necessitating a deeper dive. However, this does not mean audits should be limited to once a year.
Instead, a recommended approach is to schedule various specialized safety audits (e.g., management system audit or compliance audit) throughout the year. The final month of the year should be dedicated to a comprehensive workplace safety audit, evaluating all high-level procedures.
For example, a manufacturing company might conduct quarterly audits focusing on equipment safety, chemical handling and ergonomics, while reserving the final month for a holistic review of all safety aspects. By spacing out the audits strategically, organizations can address specific areas of concern effectively and take proactive measures to enhance safety standards.
2. Preparing for the audit in advance
The saying "failing to prepare is preparing to fail" holds particularly true for safety audits. Adequate preparation is essential for both auditors and the organizations being audited. Prior to the audit, organizations should ensure that managers and supervisors have all necessary records, documents and procedures readily available.
Let's say a construction company is preparing for a safety audit; they would need to compile records of employee training, incident reports, safety policies and maintenance logs. By having this information organized and easily accessible, the audit process becomes more efficient, enabling auditors to gain comprehensive insights and offer accurate recommendations.
The audit team itself should also prepare by reviewing previous audits specific to the area being audited, along with any recommended corrective actions. Additionally, familiarizing themselves with company, local, state and federal requirements related to the specific area of work ensures a comprehensive and thorough assessment.
3. Employing impartial, proficient auditors
To achieve unbiased results, auditors should not be individuals who work in the same environment they are inspecting. Fresh perspectives are crucial as auditors can spot issues that supervisors or managers may have unintentionally overlooked.
Because safety audits are invaluable in reshaping your safety processes going forward, it’s worth ensuring that whoever runs the audit has the necessary knowledge and experience. This means being up to date on all relevant laws and regulations, as well as being skilled in violation and hazard identification.
4. Meticulous recordkeeping
A comprehensive safety audit requires detailed and extensive recordkeeping. Before commencing the audit, the auditor must review all available incident reports related to the area being audited. This examination provides crucial insights into potential problem areas that are likely to emerge during the audit.
Detailed incident reports empower auditors to scrutinize these target areas more effectively. Additionally, using audit checklists during the audit ensures comprehensive coverage of safety objectives and relevant regulations.
For example, consider an office setting where a safety audit is being conducted; the auditor would thoroughly review incident reports related to slips, trips and falls, ergonomic issues and electrical hazards. Armed with this information, the auditor can focus on these specific aspects during the audit, taking a proactive approach to address potential risks.
5. Skillfully extracting insights from data
Once all documents, procedures, work practices and relevant equipment have been examined, the auditor consolidates the collected data to create a comprehensive, concise report that details the audited area of the organization.
This report should include comments, recommendations and corrective actions. Importantly, it should also evaluate whether the audited area meets regulatory requirements and whether there is documented proof of compliance. Furthermore, the report should discuss the effectiveness of employee training in promoting safe habits.
By following these key elements of a safety audit, organizations can pave the way for a safer future. Each step contributes to an enhanced understanding of safety processes, improved compliance and proactive risk mitigation.
Evotix's Audit and Inspection Software streamlines audits and inspections using mobile technology for real-time completion. Want to learn more? Click below!
RELATED BLOGS
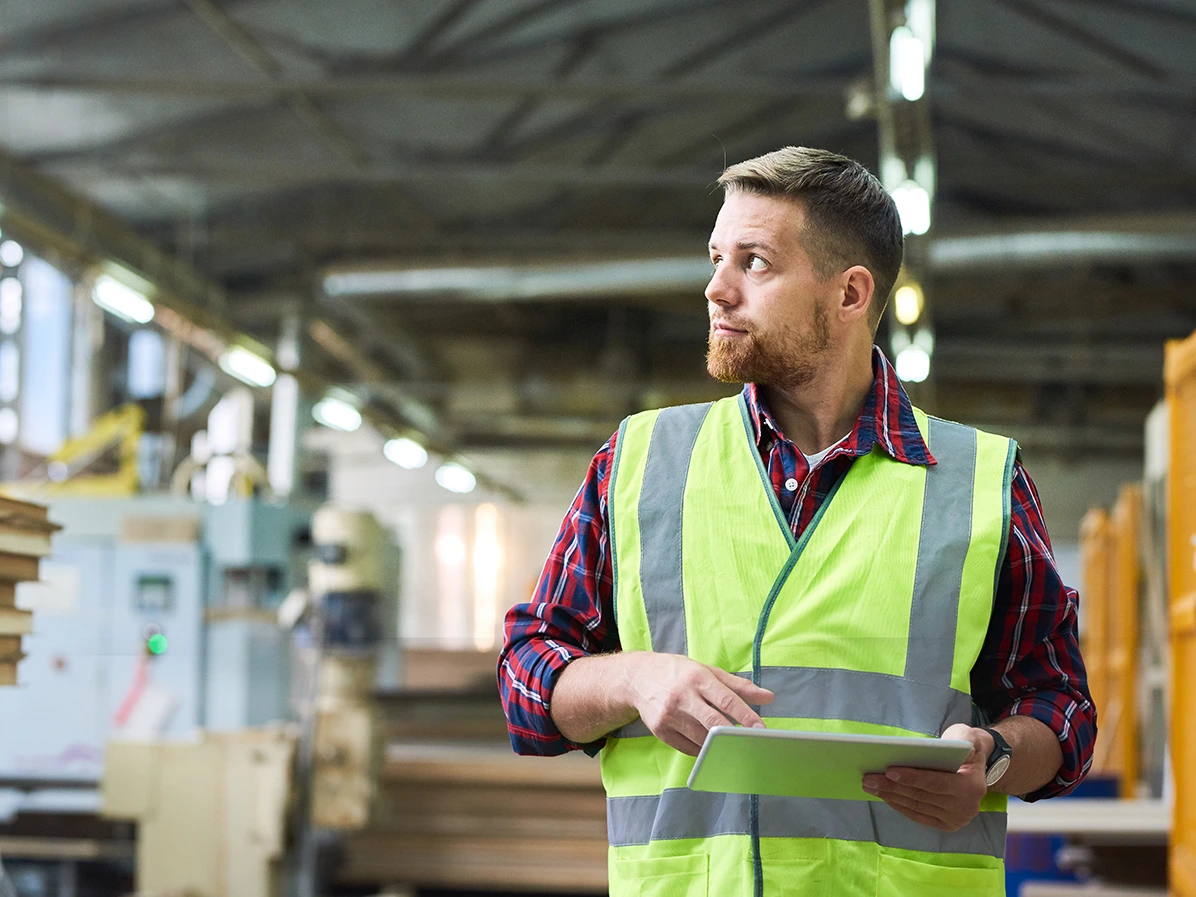
The Complete Health and Safety Audit Checklist
15 November 2024 - Evotix
Workplace health and safety is essential for every organization. Prioritizing employee well-being not only boosts productivity and morale but also improves overall quality of life. While hazards are..
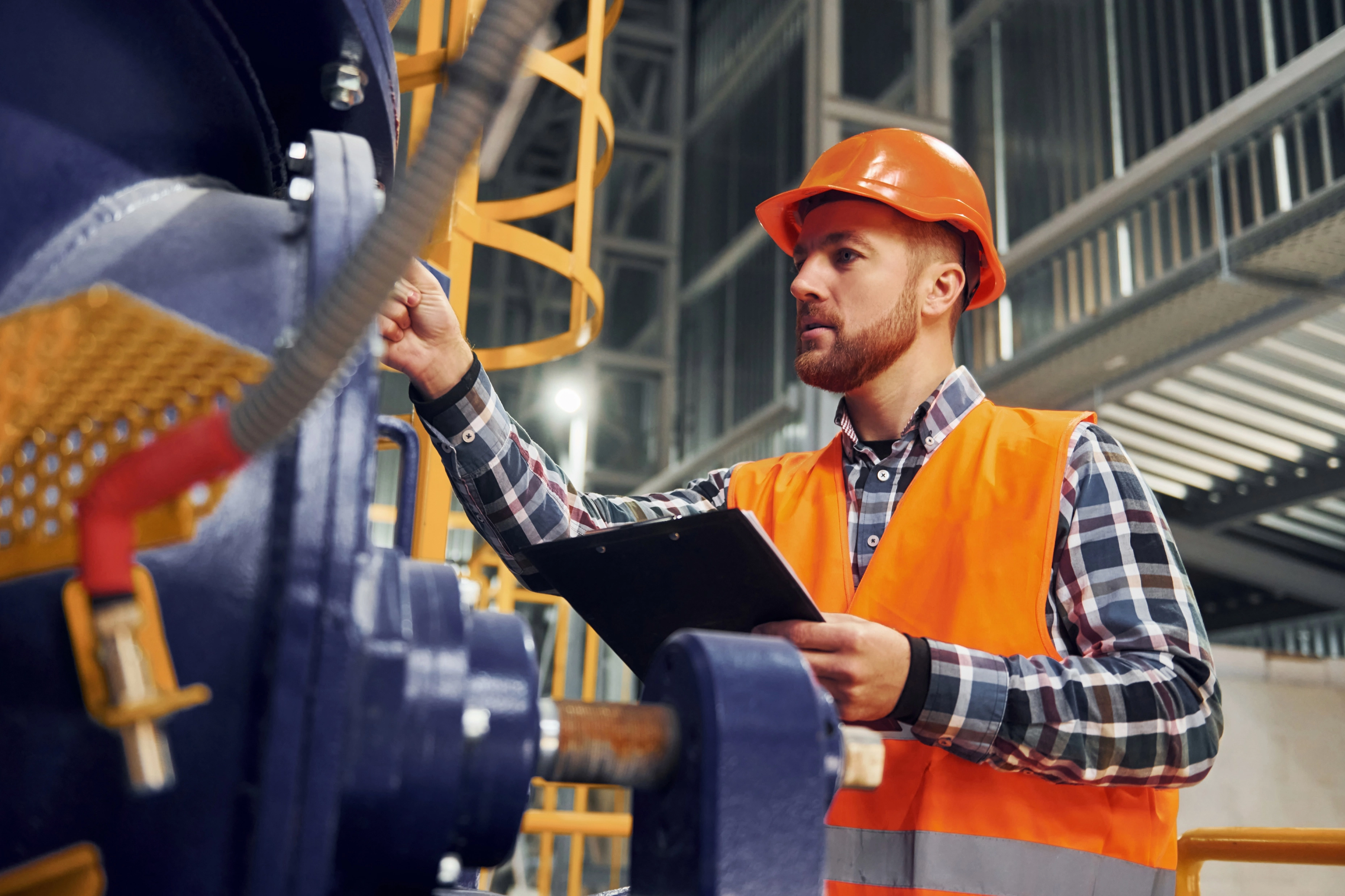
What Is the Difference Between an Audit and an Inspection?
5 December 2024 - Evotix
The complexities of health and safety management can feel daunting, especially with the constant evolution of processes and regulations. It's easy to see why terms like audits and inspections, which..
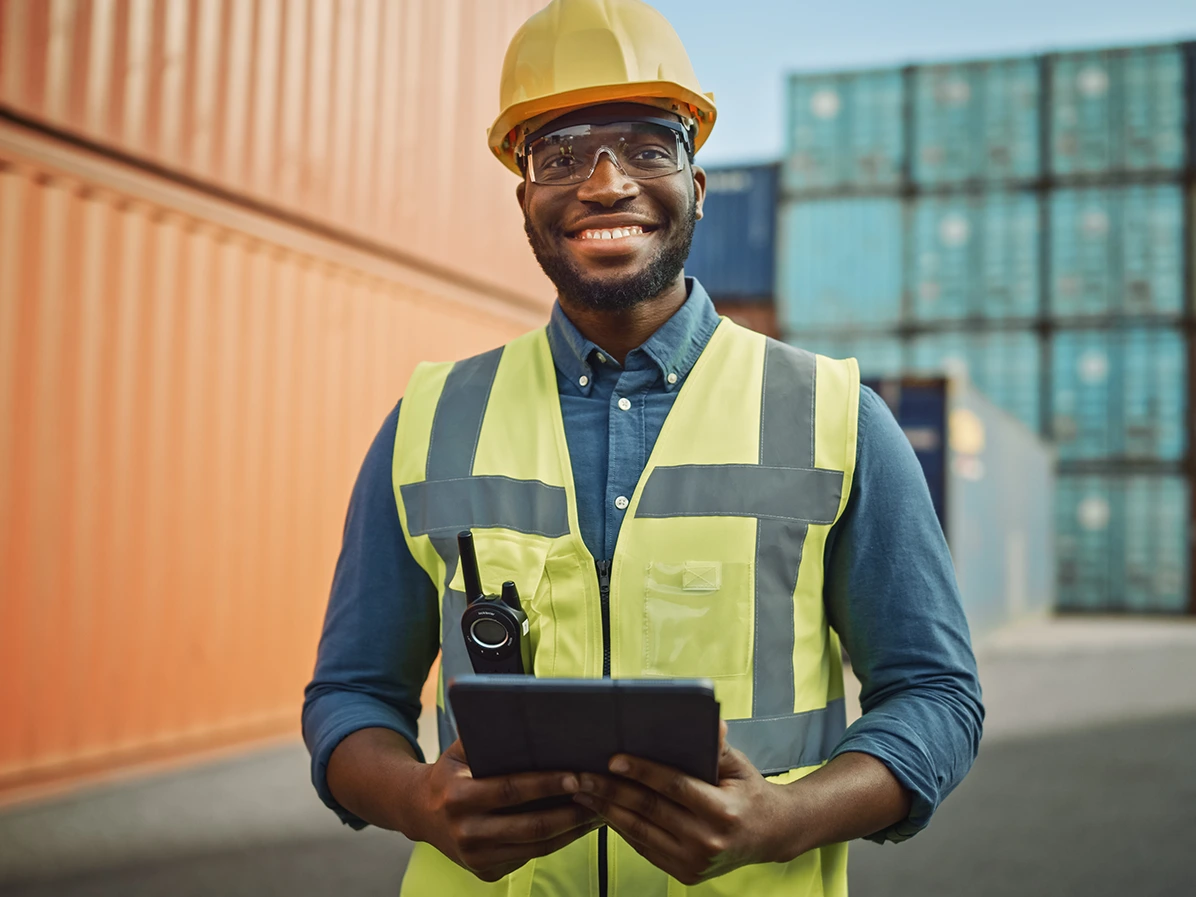
What Is an EHS Audit? Understanding the Basics
13 March 2025 - Evotix
While it’s essential to establish health and safety practices at your workplace, the work doesn’t stop there. Health and safety professionals need to constantly review safety measures to ensure..