Contents
How This Olympic Strategy Can Benefit Your EHS Program
1 August 2023 - Evotix
You're probably familiar with the saying, “It’s the little things that count.”
At the 2008 Olympics in Beijing, British Cycling used this exact concept to win 14 medals, eight of them gold.
Sir Dave Brailsford, former performance director of British Cycling and manager of UCI WorldTeam Ineos Grenadiers, has since named one of the reasons for his team’s triumphs—the 1% Factor, or the Theory of Marginal Gains.
His theory hypothesizes that tiny improvements to various aspects of a team’s strategy, when added together, can make huge differences in the outcome of a race.
What does it have to do with health and safety?
Ed Clancy, a cyclist on Brailsford’s 2008 team, recently sat down with Evotix’s Langdon Dement and Julian Taylor on our podcast, Two Bald Guys Talking Safety, to discuss the British cycling team’s Olympic successes.
“You can apply the philosophy [of marginal gains] to almost anything in life,” Clancy says.
In fact, most of us use the theory every day. When you brush your teeth, for example, you’re making a tiny improvement. Brushing for two minutes won’t make much of a difference alone, but when done daily, those tiny improvements add up to deliver you a shining bill of health from the dentist. On the other hand, if you skip daily brushing, you could end up paying through the teeth for fillings.
When it comes to health and safety, where the stakes are higher than a few cavities, the need for improvements is even greater. Whether it’s a worker reporting a near miss, a manager reading an incident report or a company removing a hazard, small actions can make big differences.
But many companies tend to focus on the big picture. They concentrate on securing sweeping health and safety programs instead of making sure the simplest procedures, like hazard reporting, are rock-solid.
How does it work?
When it comes to safety, breaking processes down into their simplest components is key. But apart from focusing on incremental wins, Clancy says teams need two things to make the marginal gains theory work: a willingness to learn and an abundance of resources.
It can be tricky for practiced workers to make changes to their routines. They know how best to do their jobs. But the theory of marginal gains teaches us that in order to make a big difference, tiny improvements must be made.
So how can companies show workers the importance of making small changes? Engagement is key.
Safety professionals know that one of the most important challenges they face is making people care about improving health and safety in their workplaces. It’s easy to become complacent, especially when management hasn’t made engaging employees in safety a priority.
Brailsford has two key engagement suggestions:
1. Instead of endlessly emphasizing your company’s health and safety goals, tap into each worker’s wants.
As Brailsford says in a video by London Business Forum, “Whether we know it or not, we’re making a calculation: What’s in it for me? I look at every individual and try to figure out what’s in it for them. If you can align what they’re doing with a group of other people behind one goal, then you’re in business.”
In safety, this might mean reminding employees that their activities outside work, like cooking, jogging or taking the kids to the park, might not be possible if they get injured at work. Making small changes to their individual routines will reduce the chance that their lives will be affected by an accident at work.
2. Give workers ownership over health and safety.
“I believe in giving people as much ownership as possible,” Brailsford says. “As human beings, we like to have an influence over what we do and how we do it.”
Teaching individuals to recognize and report hazards and incidents is the first step toward empowering them to take that ownership. The second is making it as simple as possible for them to engage with health and safety—whether that’s implementing easy-to-use software or a streamlined reporting system.
Now that you've established a willingness to learn among your employees, having an abundance of resources for them is also key. ‘Resources’ doesn’t just refer to cash. When it comes to safety, your resources are your workers, your managers, your health and safety personnel, your systems and procedures and your software.
Workers and managers can be the best resource companies have for upholding good health and safety practices. They know the job and see what others don’t see. Whether or not they’ll be helpful in implementing the Theory of Marginal Gains depends, of course, on whether your workforce is willing to learn.
Making tiny adjustments to systems and procedures—for example, making it easier for workers to report a near miss—can make all the difference.
You might choose to adjust your health and safety software solution to prompt employees to upload a photo in a hazard report. You might put up signs around the workplace reminding workers to keep their eyes open for hazards. Or you might have an extra light installed in a dark corner of the workplace. The possibilities for tiny improvements are endless!
Having successfully sent British Cycling to the podium at the Olympics, the Theory of Marginal Gains is applicable to many areas, including the world of health and safety.
We already know the little things are important when it comes to safety. Whether it’s a manager addressing a hazard report or a worker wearing PPE correctly, small actions can make a big difference but will only work if your company is willing to learn and use its resources.
To learn more about how to properly engage your workers in health and safety, check out our eBook: Putting Safety in the Hands of Your Employees
RELATED BLOGS
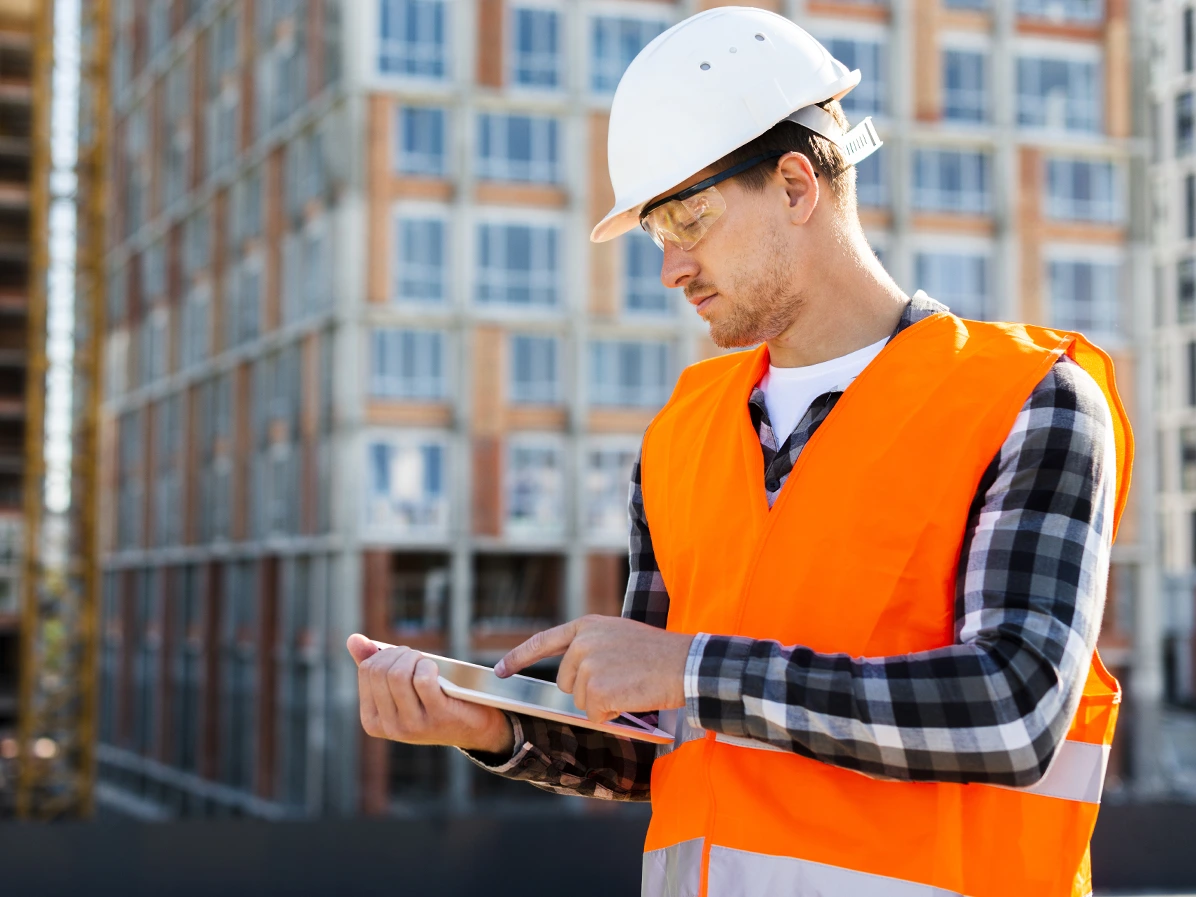
What Is Contractor Safety Management?
21 November 2024 - Evotix
Hiring skilled contractors to address workforce gaps is becoming increasingly common. However, as temporary team members, contractors often bring varying levels of skills, qualifications and..
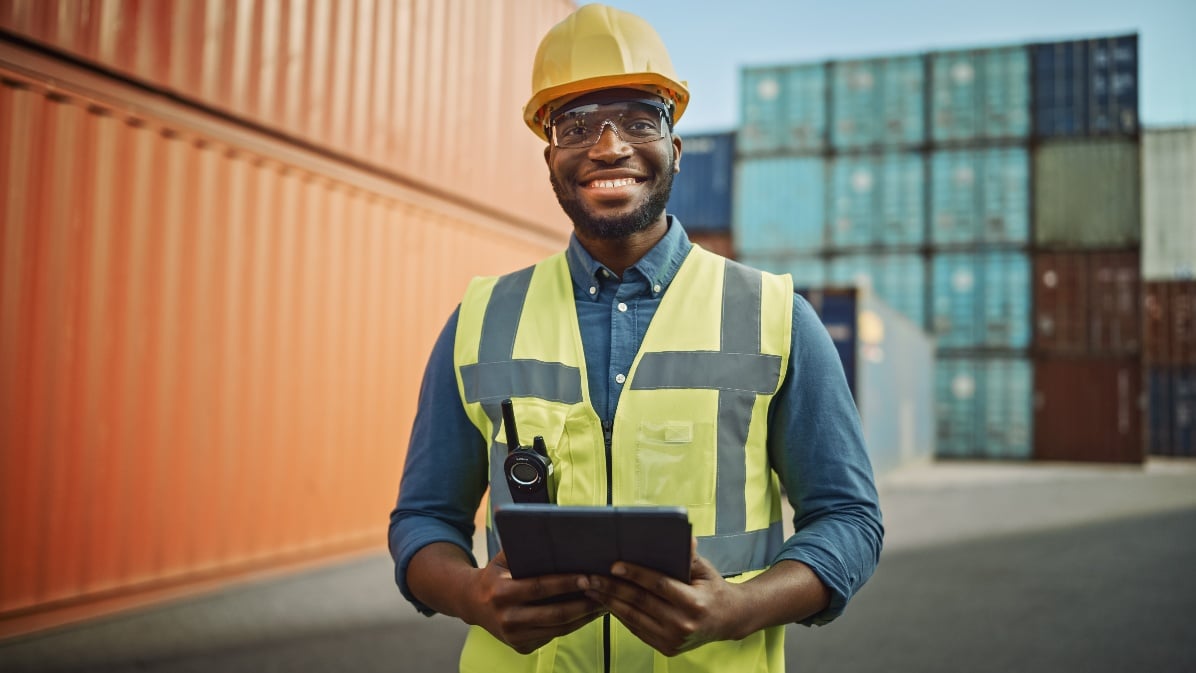
What is an EHS Manager? Today and in the Future
20 April 2022 - Evotix
For over the past decade, a big transition has been taking place in the way companies manage health and safety.
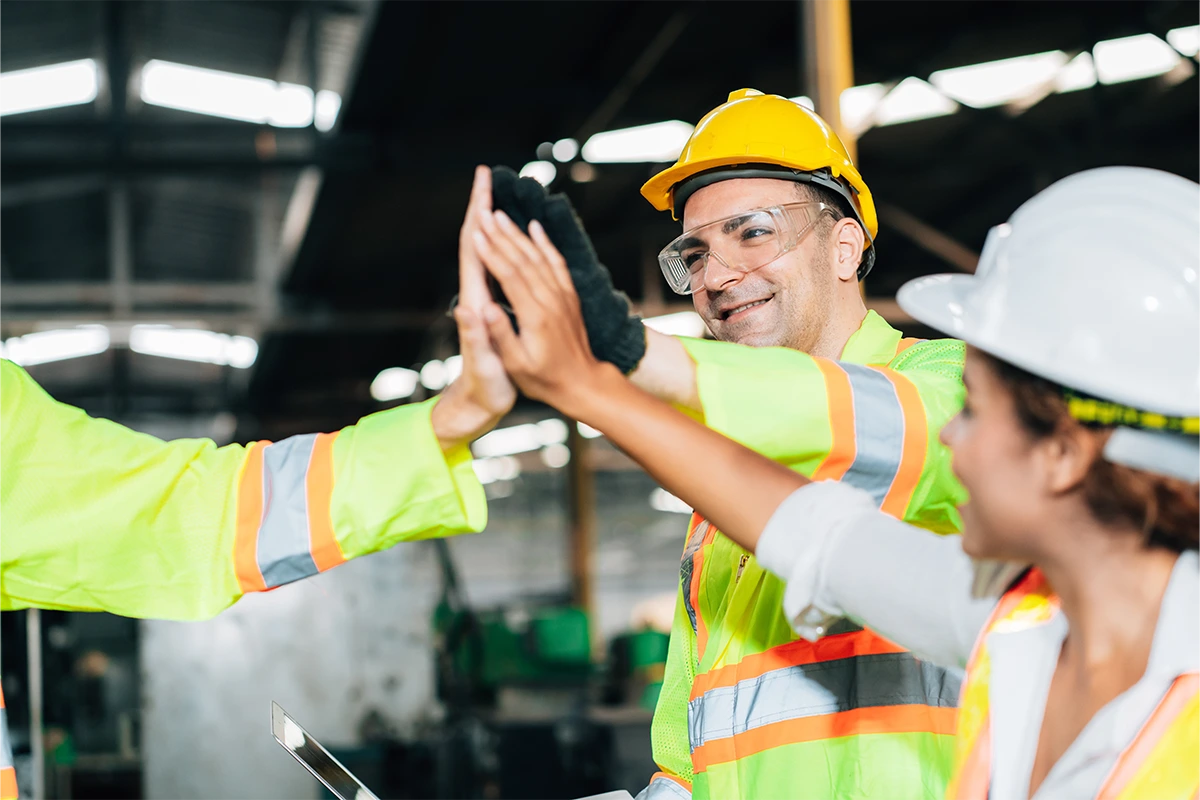
Health and Safety and HR: Working Together to Create Better Workplaces
8 September 2022 - Evotix
HR plays a major role in health and safety. Traditionally, the department responsible for a business’s success and sustainability mainly oversaw the functions of recruitment and payroll. But today,..