Contents
What To Look For When Sourcing PPE
25 April 2023 - Evotix
Personal protective equipment (PPE) is an essential part of ensuring the safety and well-being of employees. Whether you are in construction, healthcare or manufacturing, it is important to devote time and money to securing the right PPE.
However, finding the right equipment can be challenging. There is a dizzying array of options available on the market, the guidelines are subtly different for every industry subset and there are misconceptions saturating the web that make finding accurate advice tricky.
In this article, we will provide a step-by-step guide on how to source PPE for a particular industry, site or task, go over how to judge the quality of PPE ahead of committing to a purchase and share with you where reliable information can be found online to direct your inquiries.
Step 1: Identify the hazards unique to you
Before you start sourcing PPE, you need to identify the hazards present in your workplace for the specific task at hand. This will help you determine the appropriate PPE to use. For example, if your workers are exposed to harmful chemicals, you may need to provide them with chemical-resistant gloves, goggles and respirators. If your workers are exposed to biological hazards, they may not need respirators but may require masks and coveralls.
If you have multiple jobs that need different kinds of PPE, you can conduct a job hazard analysis (JHA). This involves breaking down each individual job into its basic components to better identify the hazards associated with that specific job. For further information on how to conduct a JHA, read this blog post.
Step 2: Determine the level of protection needed
After identifying all the hazards your employees are facing, you need to determine the level of protection those hazards demand. This will depend on the severity of each risk and the amount of exposure time. For example, if your workers are exposed to high levels of noise, you may need to provide them with hearing protection devices that offer a high noise reduction rating (NRR). Other workers in separate strands of your business might not need these kinds of devices or may only need a lower-rating device.
Additionally, you need to determine which of your employees require additional hazard protection. Some employees with specific health concerns or physical limitations may need specific PPE items, such as respirators, designed specifically to accommodate medical conditions.
Step 3: Consider comfort and fit
When selecting PPE, it is essential to consider the comfort and fit of the equipment. If the PPE provided is uncomfortable or ill-fitting, your employees may be tempted to wear it improperly, or even remove it entirely. Both will significantly increase the risk of injury and/or illness in the case of an incident.
Additionally, ill-fitting or uncomfortable PPE is distracting for the wearer. Having to constantly adjust or rearrange their safety equipment makes employees less productive and takes focus away from the task at hand. Therefore, it is crucial to choose PPE that properly fits every employee. When it comes to PPE, maximum comfort equals maximum compliance.
Step 4: Look for recognizable signs of quality
When sourcing PPE, it is important to look for recognizable signs of quality. Always look for PPE that meets the relevant safety standards, such as ANSI Z87.1 certifications for standard eye and face PPE. Remember, these safety certifications are only meaningful if they are set by an official regulatory body, such as OSHA, ANSI or NFPA.
Quality PPE will be properly fitted to ensure its effectiveness and should be available in different sizes to ensure the correct fit for every wearer. One-size-fits-all is often a sign of poor quality. Additionally, good quality PPE should be easy for all your employees to use without extensive training or expertise, as complex instructions reduce the likelihood of the PPE being used consistently and correctly. If training is required for any reason, good quality PPE should come with clear instructions on use, maintenance and storage.
Step 5: Don't fall for common misconceptions or mistakes
Here are some common mistakes managers make when sourcing PPE:
1. Choosing PPE based on cost and not suitability
Lower cost generally means lower quality, which means the PPE will wear out faster, is less likely to be worn correctly by employees and may not be fit for purpose – all of which leads to higher likelihood of an incident or illness and thus, higher costs.
2. Not involving workers in the selection process
Part of any JHA should include speaking with employees to learn about how they will use their PPE and what needs must be met. This conversation should continue through to any relevant PPE training or instruction for staff and managers.
3. Thinking that PPE is a substitute for engineering or administrative controls
PPE is the last line of defense, and it is essential to implement other control measures to reduce hazards whenever possible.
Step 6: Determine what works best for your team
When sourcing PPE, finding what works best for your team means making educated choices, but remaining flexible. You may have considered the specific needs of your employees, the type of work they do and the environmental conditions they work in and made what seemed like the right decision. But after evaluation, you realize that your workers are not using the PPE as you intended, or that your research did not reveal all the hazards your workers are facing.
For example, if your employees are working outdoors in the hot sun, you may have provided them with lightweight, breathable clothing and hats. An evaluation revealed that your workers are happy with the lightweight clothing, but that the hats are uncomfortable when worn for a full shift.
A manager should continually evaluate the effectiveness of the PPE they are providing their workers with and be flexible in adapting to meet changing or newly uncovered needs.
Sourcing PPE is a critical aspect of ensuring the safety of workers. By following the steps outlined in this guide, you can identify hazards, determine the level of protection needed, consider comfort and fit, look for recognizable signs of quality, avoid common mistakes and misconceptions and determine what works best for your team.
Remember, investing in quality PPE is an investment in the safety and well-being of your employees, which is always worth it in the end.
Digital asset management software allows your organization to track all pieces of PPE to ensure that equipment is ready to use. For more information, visit our solution page below!
RELATED BLOGS
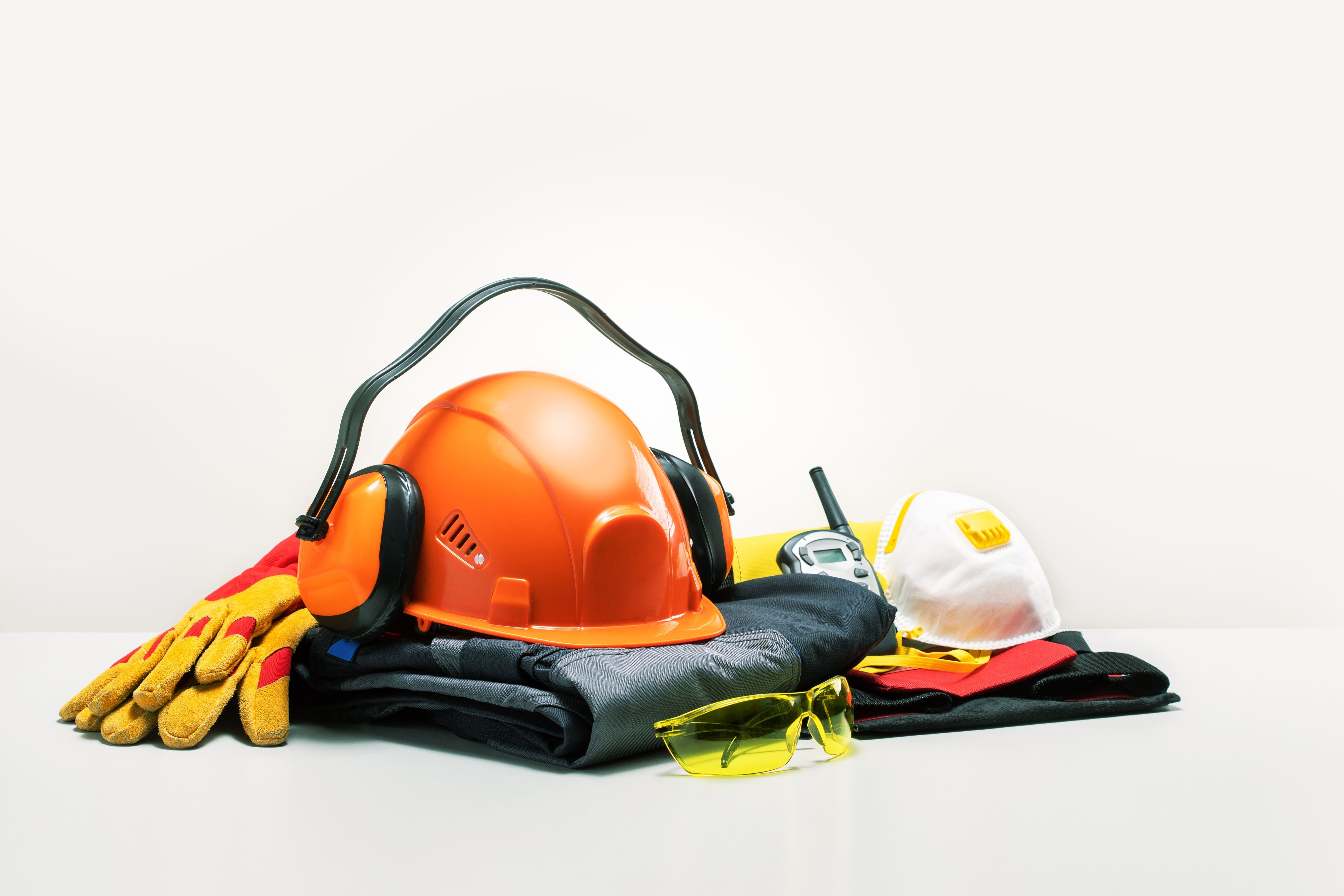
Understanding OSHA's New Construction PPE Requirements
18 February 2025 - Evotix
The Occupational Safety and Health Administration (OSHA) has recently revised standard 29 CFR 1926.95(c) for construction personal protective equipment (PPE). The final rule, which took effect on..
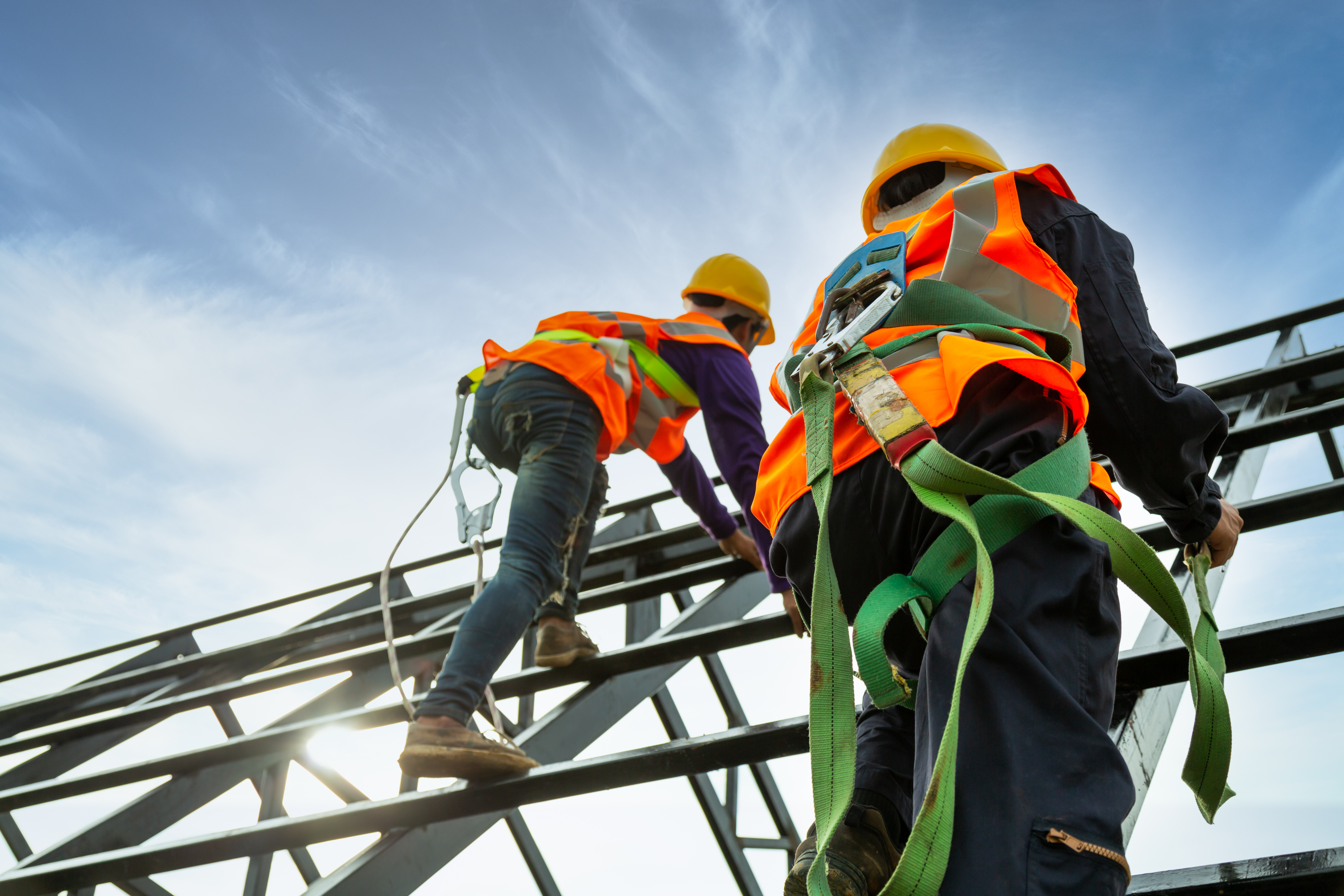
Examining OSHA’s Top 10 Most Cited Health and Safety Standards of 2023
19 December 2023 - Justin Moats & Langdon Dement
In our ever-evolving work landscape, it’s critical for businesses to stay ahead of the curve, especially in light of the Occupational Safety and Health Administration’s (OSHA) latest findings on the..
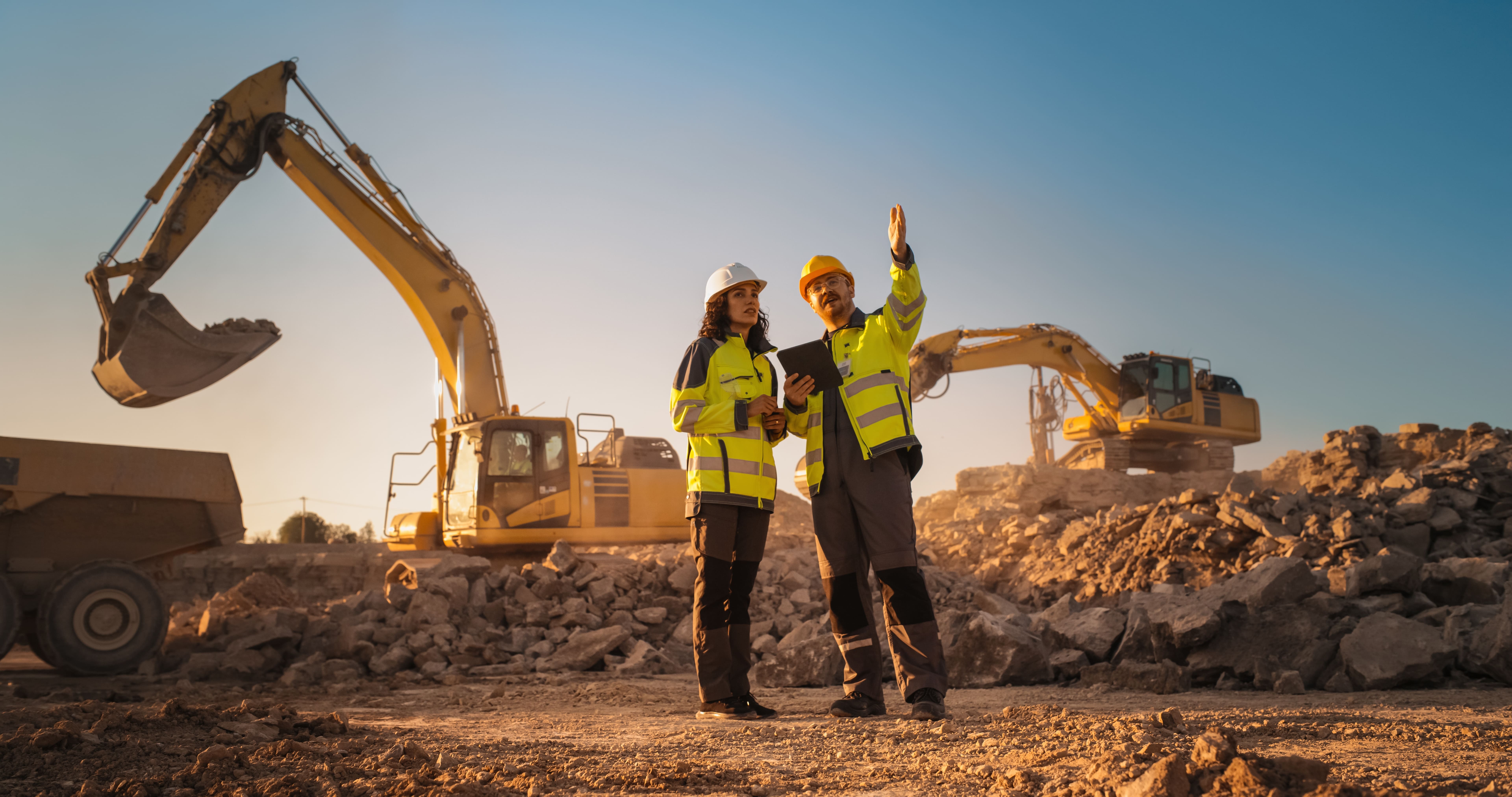
Top Hazards in the Mining Industry and How to Mitigate Them
6 March 2025 - Evotix
The mining and mineral industry presents a uniquely hazardous work environment. While technological advancements and safety regulations have significantly reduced injuries and fatalities over the..